Call us now:
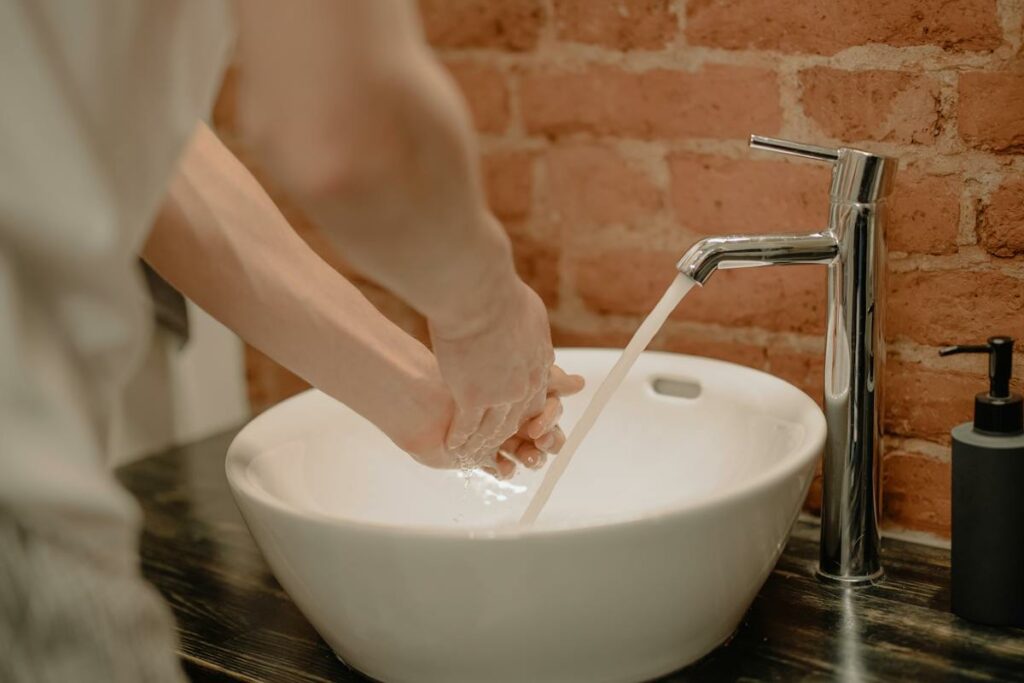
The Occupational Safety and Health Administration (OSHA) ensures US worker safety. Compliance with OSHA regulations is a legal obligation for employers and helps maintain a safe work environment. Understanding and navigating these complex regulations can be challenging, but is crucial to avoid penalties. Businesses need to understand OSHA regulations, their application to their operations, and compliance steps. This discussion offers valuable insights into OSHA compliance for businesses.
Understanding OSHA’s Role
OSHA, established by the 1970 Occupational Safety and Health Act, is dedicated to worker safety. Its mission is to assure safe and healthful conditions for workers. Its influence on workplace conditions is significant, stemming from its regulatory responsibilities. OSHA develops, interprets, and enforces safety and health standards across industries. It uses processes like risk assessment, compliance auditing, and hazard communication for enforcing its rules. Public views on OSHA fluctuate between appreciation for its protective role and criticism for potential over-regulation.
Importance of OSHA Compliance
OSHA compliance is crucial for worker safety, health, and organizational profitability. The evolving regulations reflect workplace dynamics and complexities, necessitating proactive adherence by organizations. Benefits of compliance include reducing workplace accidents and illnesses, minimizing costs, fostering a safe culture, boosting morale and productivity, and increasing employee retention. Compliance also aids in avoiding fines, penalties, and legal issues, while protecting the company’s reputation. Hence, OSHA compliance is not just a legal obligation but a strategic investment for a safe, healthy, and productive workplace.
Decoding OSHA Regulations
Understanding and complying with OSHA regulations requires ongoing analysis and interpretation due to their complexity and continuous evolution. This involves dissecting the statutory language, examining historical context, and reviewing relevant case law to understand their workplace safety implications.
The constant evolution of OSHA regulations, marked by increasing specificity and clarity, reflects the agency’s commitment to adapting to industry changes. However, this poses challenges for organizations to stay updated and adjust their safety protocols.
Decoding OSHA regulations is an incessant process requiring a regulatory-focused approach, an analytical mindset, and understanding their relationship with other laws and industry standards. This helps to ensure workplace safety and protect organizations from non-compliance penalties.
Steps to Achieve Compliance
Compliance with OSHA regulations involves two key steps: safety protocol implementation and regular compliance audits. Safety protocols create a secure work environment in line with OSHA guidelines. Compliance audits assess the efficacy of these safety measures, ensuring continued alignment with OSHA standards and enabling necessary adjustments.
Implementing Safety Protocols
Implementing safety protocols, a key step for OSHA compliance, demands a meticulous approach and deep knowledge of regulations. It encompasses strategic use of safety equipment and risk assessment methods. Safety equipment like Personal Protective Equipment (PPE) significantly reduces workplace hazards, given its proper usage and maintenance. Risk assessment methods, the analytical foundation of safety protocols, identify potential hazards, evaluate their severity, and prioritize control measures. These protocols, ensuring OSHA standards compliance, promote a safe, healthy work environment. They require regular reviews and updates, aligning with the evolving regulatory landscape.
Regular Compliance Audits
Regular compliance audits are crucial for OSHA regulation adherence, allowing businesses to pinpoint and rectify non-compliance areas. Despite their complexity and potential to increase compliance costs, these audits can be efficiently managed by:
- Documenting safety procedures and protocols meticulously.
- Training employees comprehensively on OSHA regulations.
- Scheduling consistent audits for continuous compliance.
- Engaging a compliance officer or consultant for audit guidance.
This diligent audit approach, combined with OSHA regulation understanding, helps mitigate non-compliance risks and manage costs.
OSHA Inspection Preparedness
Understanding the OSHA inspection process, preparing the workplace comprehensively, and addressing inspection findings aptly are essential for OSHA inspection readiness. Detailed knowledge of OSHA regulations and strategic compliance approach are required. These elements ensure your organization’s OSHA inspection preparedness.
Understanding OSHA Inspection Process
In the occupational safety field, understanding OSHA inspections is vital for regulatory compliance and enhancing a company’s readiness. It’s important to know about inspector qualifications and possible outcomes of inspections.
The inspection process includes:
- Opening Conference: The OSHA inspector clarifies the inspection’s purpose and scope.
- Walkaround: The inspector examines the facility to identify potential safety hazards and violations.
- Closing Conference: The inspector presents findings, discusses potential abatement strategies, and explains possible penalties.
- Inspection Report: OSHA may issue citations post-inspection, listing violations, suggested penalties, and abatement needs.
These steps promote compliance, improve safety, and reduce potential penalties.
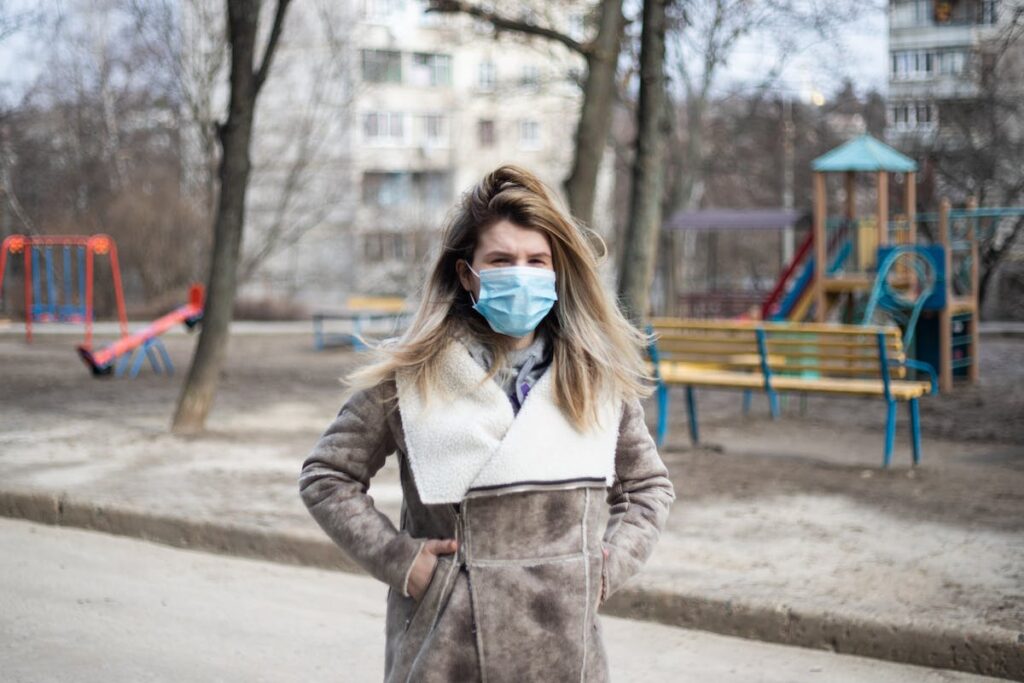
Preparing for Workplace Inspection
To comply with OSHA inspections, a strategic preparation plan is vital. This plan should cover Inspection Anxiety Management, educating employees about inspections, and dispelling fear. It should also handle Inspection Day Logistics, coordinating documents, identifying hazards, and assigning a team for inspection. The plan should be both reactive, addressing immediate safety issues, and proactive, preventing future risks. With careful planning and preparation, the inspection’s impact can be minimized, ensuring regulatory compliance.
Addressing Inspection Findings Properly
Upon receiving OSHA inspection findings, address each issue promptly and meticulously for ongoing compliance with regulatory standards. The process includes:
- Finding Evaluation: Analyze OSHA’s report to comprehend each non-compliance issue’s nature and severity.
- Corrective Action Plan Development: Design detailed plans for each issue remediation, outlining tasks, responsible parties, and timelines.
- Communication Strategy Implementation: Disseminate findings and corrective actions to related stakeholders, including employees and management.
- Progress Monitoring and Verification: Regularly oversee progress and confirm successful corrective action implementation.
These actions, when efficiently performed, facilitate OSHA compliance, ensuring a safer, healthier work environment.
Handling OSHA Violations
Swift and appropriate handling of OSHA violations is vital for upholding a safe, compliant work environment, impacting an organization’s finance and operations. The severity and type of violation determine the outcome, ranging from a warning to substantial fines or even operation shutdowns. An effective action plan rectifies and prevents reoccurrence of the violation.
OSHA regulations ensure Employee Rights, which include a safe workplace, hazard-reporting without retaliation fear, and access to OSHA inspection outcomes. Proper comprehension of these rights is integral for correct violation management.
Training Requirements for Employees
OSHA’s training requirements mandate employees to be knowledgeable about workplace hazards, their recognition, and mitigation procedures. This training, which should be practical, ongoing, and specific to workplace hazards, is a compliance requisite and a key to a safe, productive work environment.
To implement an effective training program, employers need to:
- Identify possible workplace hazards.
- Create an all-inclusive training plan on hazard recognition and prevention.
- Regularly update training to reflect workplace or regulatory changes.
- Promote active employee participation in training, enhancing a safety and empowerment culture.
Adherence to these requirements fosters a proactive safety culture and ensures employees are well-equipped to handle risks.
Implementing Workplace Safety Measures
Implementing robust safety measures in the workplace is integral for OSHA compliance. Key aspects include strategic safety equipment deployment, potential hazard identification, regular equipment maintenance, and clear safety procedures establishment. Equipment like fire extinguishers, first-aid kits, and personal protective equipment (PPE) such as safety goggles, hard hats, and safety shoes are crucial in accident prevention.
Appropriate safety signage guides employee behavior, preventing accidents. Safety procedures communication is essential, keeping staff updated on work environment changes or OSHA regulations.
Creating a safety-conscious culture encourages employees to report potential hazards, ensuring thorough investigation of raised concerns. It’s vital for maintaining a safe workplace environment.
Recordkeeping for OSHA Compliance
Precise recordkeeping is crucial for OSHA compliance, serving as both proof of safety regulation adherence and a hazard identification tool. However, recordkeeping errors can invalidate these records and risk non-compliance. Recognizing these errors and employing corrective strategies is essential for enhancing OSHA compliance.
Importance of Accurate Recordkeeping
Accurate OSHA compliance recordkeeping is crucial for:
- Trend identification in workplace injuries or illnesses to develop preventative strategies.
- Providing proof of OSHA regulation adherence during inspections.
- Facilitating safety discussions between employees and management.
- Enhancing accountability by monitoring safety procedure efficacy and employee training.
Utilizing recordkeeping software and promoting employee participation optimizes this process.
Common Recordkeeping Mistakes
Common OSHA recordkeeping mistakes include inaccurate data entries, delayed updates, and not keeping records for the needed duration. Using recordkeeping software can minimize these errors by automating data input and tracking updates. These systems alert when data is incomplete or record retention deadlines are near. Regular audits, staff training, and standard forms can also improve record accuracy. Addressing these mistakes can boost OSHA compliance, prevent penalties, and promote safety.
Improving OSHA Compliance Records
Improving OSHA compliance records requires four key steps: executing regular audits, utilizing standardized forms, training staff, and updating safety protocols.
- Audits: Routine audits detect and correct compliance gaps, ensuring OSHA regulations adherence.
- Forms: Standardized forms streamline recordkeeping and minimize errors.
- Training: Staff education on OSHA recordkeeping roles and responsibilities eliminates compliance issues.
- Updates: Regular safety protocol revisions maintain effective OSHA compliance records.
These steps not only bolster safety and risk reduction but also foster a safety-first work culture.
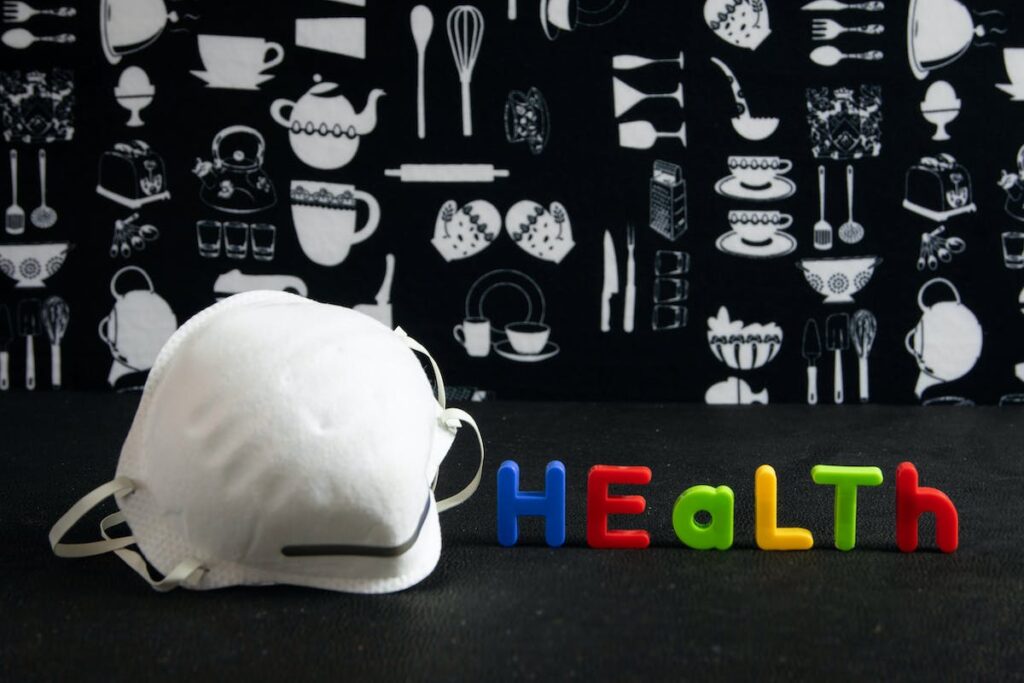
Reporting Workplace Incidents
To comply with OSHA regulations, businesses must promptly and accurately report all workplace incidents. These reports offer crucial data on organizational health and safety issues. Implementation of effective incident investigation techniques is essential. This involves identifying the incident’s root cause, determining its sequence of events, and initiating corrective actions to prevent future similar occurrences.
Additionally, providing employees with whistleblower protections is critical. This promotes transparency, enabling employees to report unsafe conditions without fear of reprisal. OSHA’s Whistleblower Protection Program safeguards employees who report workplace hazards, enhancing workforce safety and health.
Understanding OSHA Penalties
Grasping OSHA penalties aids in adhering to workplace safety norms. This segment elucidates OSHA violation categories and penalty computation method. Such understanding enables businesses to comply with regulatory mandates and lessen possible violations.
OSHA Violation Categories
In occupational safety, four primary OSHA violation categories exist, each with unique penalties for non-compliant businesses. Understanding them aids in creating effective prevention strategies and comprehending violation repercussions.
- Willful Violations: Intentional disregard for OSHA regulations, attracting the highest penalties.
- Serious Violations: Occurrences with a substantial chance of causing death or severe physical harm, and the employer’s lack of reasonable preventive efforts.
- Repeated Violations: Previously cited infringements by an employer.
- Other-than-Serious Violations: Directly related to job safety and health, yet less likely to cause death or severe physical harm.
Penalty Calculation Process
OSHA violation penalties are calculated through a detailed process that accounts for the violation’s gravity, the business’ size, and its compliance history. This process can significantly impact a business’s operations, reputation, and profits. Therefore, businesses should adopt penalty mitigation strategies like proactive safety audits, hazard correction, and employee training. These strategies not only improve OSHA compliance but can also lead to penalty reductions. This highlights the necessity of companies being proactive in maintaining OSHA compliance.
Compliance Assistance Resources
Compliance Assistance Resources aid in OSHA regulation adherence. Despite available resources, their limitations may challenge workplace safety. Evaluating these resources is critical for effective application within specific organizational constraints. Four key resources include:
- OSHA eTools: Web-based training tools for guidance on OSHA standards, covering various workplace conditions and hazards.
- OSHA Safety and Health Topics Pages: Pages providing information on work hazards and related OSHA standards.
- On-Site Consultation Program: A free service for small to medium businesses, aiding in hazard identification and safety system improvement.
- Training and Education: OSHA-provided training for understanding and complying with OSHA law responsibilities.
These resources can enhance an organization’s OSHA compliance when applied effectively.
Case Studies: OSHA Compliance
OSHA compliance case studies enlighten us on effective regulatory standards navigation by organizations, guaranteeing safety and reducing liabilities.
A manufacturing firm, following OSHA’s identification of safety hazards, exemplifies this. The firm instituted a robust safety program, including employee training and regular audits, resulting in reduced accidents and liabilities. This illustrates the efficacy of OSHA regulations in industries.
Similarly, a construction firm, initially daunted by OSHA complexities, employed a safety officer to ensure protocol adherence. This led to a safer work environment and fewer OSHA violations, emphasizing the importance of expert staff in compliance challenge navigation.
These cases highlight OSHA compliance’s significance and its positive industrial impact. They also show the potential challenges in standards adherence, underscoring the need for comprehensive understanding and application of OSHA regulations.
Role of Health and Safety Officers
Health and Safety Officers are central to OSHA compliance, tasked with creating, implementing, and enforcing safety programs. Their role mitigates workplace injuries and illnesses, ensuring OSHA regulation conformity.
Officer Certification Process is integral, providing essential skills and knowledge through rigorous training and assessments on workplace safety and health.
Challenges faced by Safety Officers include staying updated with OSHA regulations, creating effective safety programs, addressing non-compliance, and managing potential hazards.
In summary, a Health and Safety Officer’s duties include:
- Crafting and executing safety programs.
- Enforcing OSHA regulations.
- Undertaking Officer Certification Process to preserve knowledge and skills.
- Effectively overcoming Safety Officer’s Challenges.
Building an OSHA Compliance Plan
Developing an OSHA compliance plan is vital for Health and Safety Officers. The plan aims to apply OSHA regulations in the workplace, striving to exceed regulatory standards for employee safety and health.
The initial step in the process is risk identification. The plan should facilitate hazard assessments, implement safety protocols, and offer employee training to mitigate potential risks. Including employees in risk identification is essential due to their firsthand knowledge of safety issues.
The subsequent step involves strategies for employee involvement. Their active participation in safety management fosters a safety culture and reinforces commitment to OSHA standards. Employee roles may include safety committee involvement, safety audit contributions, and participation in continuous safety trainings.
Frequently Asked Questions
How Often Are Osha’s Regulations and Standards Updated?
OSHA’s regulations and standards update timeline is dynamic, driven by technology changes, industry practices, and worker safety needs, not operating on a fixed schedule but updating as necessary.
What Are the Specific OSHA Guidelines for Industries Like Construction or Chemical Manufacturing?
For industries like construction and chemical manufacturing, OSHA guidelines mandate comprehensive safety training and procedural adherence. These directives require proper hazardous materials management, safety equipment utilization, and strict compliance with safety protocols.
How Does OSHA Handle Anonymous Reports of Workplace Safety Violations?
Upon receiving an anonymous safety violation report, OSHA activates its Whistleblower Protection measures. These measures involve a thorough analysis, regulatory oversight, and required actions to ensure both worker safety and compliance with regulations.
What Are Some Examples of Workplace Situations That OSHA Doesn’t Cover in Its Regulations?
Workplace situations not governed by OSHA include mental health disorders, stress-related conditions, and non-specific ergonomic issues.
Does OSHA Provide Any Grants or Financial Assistance to Help Businesses Comply With Its Standards?
OSHA offers funding, including training grants, consultation programs, and cooperative programs, to aid businesses in standard compliance, thereby promoting workplace safety.
Conclusion
OSHA compliance, integral to employee well-being and workplace environment, involves understanding OSHA’s regulations, preparing for inspections, and developing a compliance plan. Resources and safety officers significantly contribute to this process. Practical case studies enhance the understanding of the importance of adhering to OSHA guidelines. Hence, establishing a safety and health culture within organizations is essential.